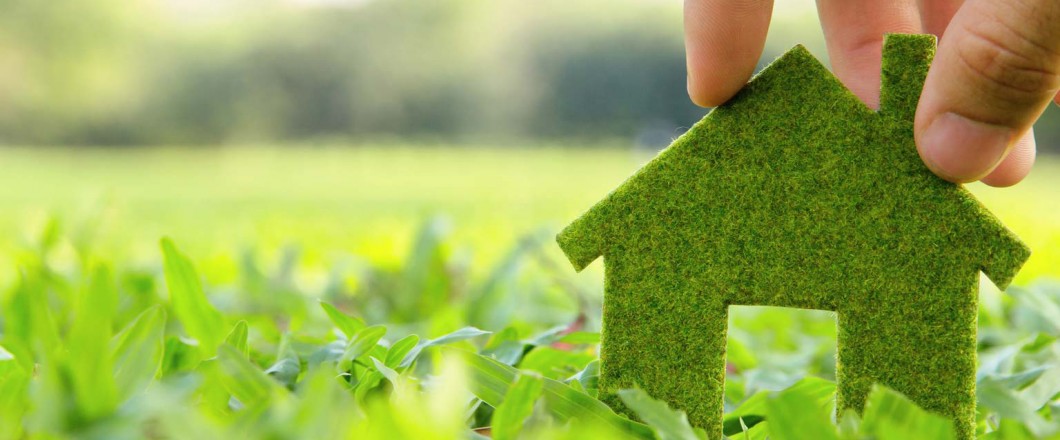
Today pultruded fiberglass sills represent an innovative and cost-effective solution for private buildings and not only. The reasons which have determined their merited success are several and also involve the thermal insulation, a typical property of composite materials.
This is an aspect which should not be overlooked within comfortable built environments, but also as far as the value of the property is concerned, where there are windows and doors with pultruded fiberglass sills, a choice that contributes to obtain CasaClima certifications: this is a guarantee to environmental sustainability of buildings.
The pultruded fiberglass sills allow to appreciate a significantly higher thermal insulation than aluminium, a metal with which we produce profiles that have greater physical dimensions and need more treatments to optimize the lifespan of windows and doors.
If you also consider that pultruded sills do not require any maintenance and do not need a double and triple chamber to obtain an optimal thermal insulation, you’ll quickly understand that if you choose them a number of advantages are offered from a practical point of view, but also from the aesthetic one: two fundamental aspects for the end user.
Thanks to pultruded fiberglass sills is possible to obtain an excellent conciliation between the energy saving, living comfort, lifespan of the product and final aesthetics.
In this respect it is recalled that the importance of thermal insulation, referred to as the central criterion for different realities where pultruded sills are installed in different contexts, offers a really interesting picture of the situation.
All this is a sign of changed times in relation to the awareness of the value of sustainable constructions, an excellence in this sector that has still a lot to say about to those who want to find out the advantages thanks to products, such as pultruded fiberglass sills.
Read More